The traditional use of methyl bromide fumigation soon will be phased out as a means of controlling pests in food-processing facilities. But, what will take its place? What are the viable options and how successful will they be as replacements for plant fumigation?
This article discusses the alternatives for controlling pests within grain related food-processing plants, including the use of heat and its related considerations.
THE FUMIGATION PROCESS. Methyl bromide fumigation of food-processing plants sometimes involves a pest management company to introduce the fumigant into the facility two to four times a year. This process typically requires a complete plant evacuation and shutdown. Normally such fumigations are scheduled for extended holiday weekends.
Replacing methyl bromide requires a systems approach including a combination of preventive and treatment practices. This integrated pest management approach offers a comprehensive solution that goes beyond a direct chemical-for-chemical replacement fumigant to attack unwanted insect pests.
One objective of any IPM program is to eliminate the living and egg-form population of targeted insects. Generally, the targeted insects vary from plant to plant depending on the products being processed. But, it is certain that the target list will include one or more of the "dirty dozen" of undesirable pests. (See list on page 76.)
Many food processors, especially those involved with grains, are seeking alternatives to chemical fumigation. Some research suggests using various solutions, including genetic mutations as a means of control. Most research focuses on the insects’ environment, how they live, survive, multiply and die.
Insects have exoskeletons and are adversely affected by low moisture and high temperatures. It is proven that insects exposed to temperatures in excess of 125°F (typically), with low humidity, will result in a high mortality rate of targeted insects.
HEAT AS AN OPTION. The food-processing industry has used heat treatments for insect control for many years. With the phase-out of targeted chemical fumigants, heat may play an increasing role. Heat treating a production facility works similar to a self-cleaning oven in our homes, but on a much larger scale.
The process is to isolate and seal the area to be heat treated and slowly elevate the temperature (usually 10°F per hour to avoid facility/structural expansion problems). Once elevated to between 125 to 140°F, the temperature is held steady to "cook" for an additional 24 hours. After the "cook," the structure is allowed to cool to ambient conditions.
The higher temperature (140°F) may be needed to ensure that the "lethal heat" of 125°F penetrates the cracks, crevices and cavities where bugs may seek protective shelter. Temperature sensors can be utilized to monitor the temperature in the heat treating area. The building conditions are transmitted to a central data acquisition point to log area temperatures and determine whether automatic or manual temperature adjustments are necessary. The heat-treating cycle may range from 24 to 72 hours. The heat treatment cycle will vary depending on the building’s structure composition and the outside ambient conditions.
During the heat treatment, the insects will attempt to migrate to cooler areas. Therefore, adjacent spaces not being heated need to be isolated by sealing/masking, applying residuals, sticky strips and/or diatomaceous earth, etc., to ensure no departure or escape routes are available.
WHAT HEAT SOURCE? Energy management specialists, working with pest management companies, have found heat treatments to be efficient and cost-effective. Several heat generating options, such as electric resistance, natural gas, propane and steam, are available.
Electric resistance heat is a viable alternative for small, isolated areas. An extensive system, though, would require prohibitive wiring requirements and electric resistance heat is, typically, not cost effective. There also is a concern for fires or explosions because of the high electric element temperatures. The flash point for most flour products is around 850°F, potentially less than the electric element’s surface temperature. Electric resistance heat therefore is minimally used as a source for heat treatment.
Natural gas and propane are other heat sources. Direct fired gas heaters introduce some of the same concerns as electric resistance heaters. The potential for fires or explosions still exists. Additionally, products of combustion, such as carbon monoxide, must be monitored. Moisture is also added to the area being treated. Recall that elevated temperature, along with low humidity, are key factors affecting the mortality rate of the insects.
Of the heat options available, many believe that steam heat is a viable choice. Of course, one must consider whether there is an existing steam system and whether the steam distribution system includes the area to be heat treated.
Most food-processing plants have steam systems in place. Steam coils and unit heaters are being used to provide heat for comfort and process requirements. With proper installation and controls, steam heat is an efficient option for heat-treating the facility. Even without an existing steam system, new installations can be cost effective because of the flexibility and adaptability of steam for energy distribution. Portable steam generating systems can be utilized without the overhead of installing a central boiler plant operation. This allows for refined solutions directed toward areas requiring special attention, thus reducing capital expense.
Steam heat does not add humidity to the area being treated. Elevating temperature lowers the relative humidity levels. As mentioned previously, this aids in increasing the effectiveness of the heat treatment. As the temperature in the heat-treated area returns to normal, so does the humidity level.
COST CONSIDERATIONS. The cost of steam heat treating as part of an IPM program can vary widely from plant to plant. Variables impacting costs are:
1. The area of exterior walls to be heat-treated.
2. The plant location and overall climatic conditions, including prevailing winds relative to the structure.
3. The building volume and whether treatment will be on single floors, multi-floors or an open mezzanine design.
4. The building construction and type of insulation in walls and ceilings.
5. The area and construction of windows.
6. The mass, materials of construction and relative position of equipment located in the space to be heated.
7. Availability of a steam source and the infrastructure including piping and electrical wiring. A feasibility assessment by an outside source may be required if in-house engineering is not available.
8. Whether there is a condensate return system.
9. Electrical access, current/voltage requirements. Higher voltage/phase will help to reduce wire gauge sizes and amperage draw. Any explosive/hazardous concerns are cost and safety topics that must be addressed.
10. The availability of wall and floor space to mount heating units.
The author is a senior applications specialist, Armstrong Heat Transfer Group, Three Rivers, Mich. He can be reached at jsmith@pctonline.com. For more information, visit www.armstrong-intl.com.
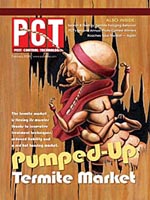
Explore the February 2004 Issue
Check out more from this issue and find you next story to read.
Latest from Pest Control Technology
- Orkin Helps Local Youth Sports Program Design a ‘Killah’ New Logo
- ABC Home & Commercial Services Celebrates 75 Years in Business
- NPMA Academy Announces Full Schedule
- Truly Nolen Promotes Marchello, Christopherson and Bolton to Managerial Positions
- TruGreen Announces 2024 List of Top 20 U.S. Buggiest Cities
- Why PMPs Use Rodent Bait Stations
- NPMA’s Women’s Forum Encouraged Female Leadership, Growth Opportunities in Pest Control
- GoPest Expands to Birmingham and Huntsville (Ala.)