
As pest control professionals, our equipment is our bread and butter. This is true whether you are the manager of a big firm with 100+ vehicles or an owner/operator with one truck. Don’t wait until your phone starts ringing off the hook this spring to get your pest control equipment in great shape.
Use the slower time at the start of the year to ensure your pest control equipment is in tip-top shape for your busy season. These six tasks are all things that should be done anyway, so you might as well do them when your business is slower and when they will not negatively impact your customers and your schedule.
1. Inspect. Use slower periods to perform thorough inspections of your vehicles, power sprayers, manual sprayers, etc. Is everything clean, in the proper place and in good working order?
2. Clean it out. Run clean water through power sprayers, hand sprayers and backpack sprayers to prevent chemical buildup. Inspect and clean out spray tanks. Thoroughly clean filters and replace bad filter screens if necessary.
3. Preventive Maintenance. Slow periods are a great time for preventive maintenance (PM). Because of hard use and harsh chemicals, all pest control equipment needs maintenance. Don’t wait for equipment to break or wear out. Service it now so you don’t have downtime and missed appointments during your busy season. If you don’t know what PM is required, ask your supplier for advice.
4. Prioritize and Plan. Review all your equipment to identify your priority items. For example, if you use your hand sprayer every day and you can’t service your customers without it, this is a priority. Figure out a way to keep a backup so when your primary fails, you are not canceling appointments.
5. Don’t Forget the Parts. If you have been using a critical piece of equipment for a while, you should have a pretty good idea of what parts will fail during the year. Keep these parts on hand to minimize downtime and missed appointments.
Think of parts in two categories: vehicle and office. Lots of common equipment issues can be fixed easily in the field. These parts should be kept in the vehicle to save time. For example, on hand sprayers, tips and tank gaskets wear out regularly, but they can be easily replaced in the field. Conversely, the valve cable that runs through the hand sprayer wand requires wrenches and more time, so this replacement part should be kept at the office.
6. Training. Use slower periods for training. Truck and equipment inspections will identify training opportunities. Equipment training will save you money and prevent downtime. It is important to also remember that just because you trained “Joe” on day one, it doesn’t mean “Joe” is still doing it the way you want him to do it. PMPs can never do too much safety training.
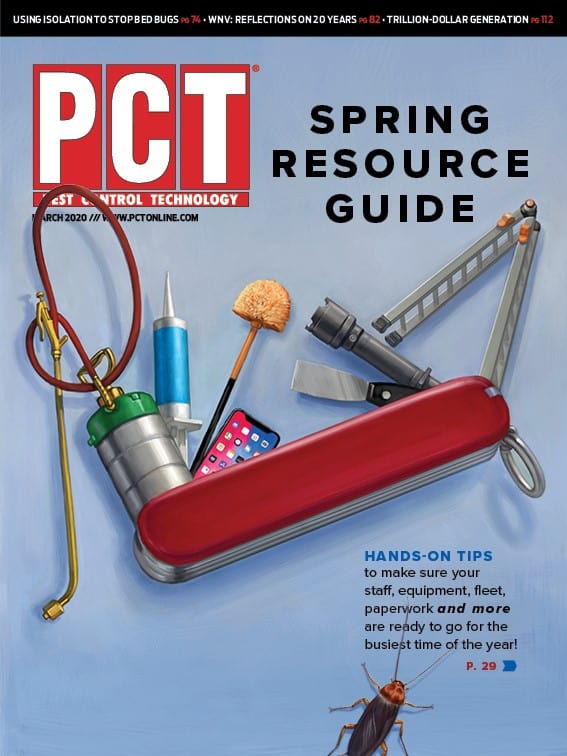
Explore the March 2020 Issue
Check out more from this issue and find your next story to read.
Latest from Pest Control Technology
- SiteOne Hosts 2024 Women in Green Industry Conference
- Veseris Celebrates Grand Reopening of the Miami ProCenter
- Rollins' 2024 Second Quarters Revenues up 8.7 Percent YOY
- Fleetio Go Fleet Maintenance App Now Available in Spanish
- German Cockroach Control Mythbusting
- Total Pest Control Acquires Target Pest Control
- NPMA Workforce Development Shares Hiring Updates
- Certus Acquires Jarrod's Pest Control