

All photos by Andrew Greess
Each week, our pest control equipment repair facility sees scores of equipment problems. The amazing thing we notice is that so many of these problems are completely preventable. Each one costs our clients time and money.
For pest management firm owners/operators, a little attention to some of these issues will make your day go much more smoothly. For supervisors/managers of larger companies, some of these issues are training opportunities that you can share with your staff.
We frequently categorize and share these issues with our clients to identify training and improvement opportunities. Here are some of the things our pest control equipment repair shop sees regularly…and how you can prevent these issues from happening at your firm.
1. Not Enough Time or Money.
Like so many things in life, we seem not to have the time or money to do it right, but we somehow find the time and money to do it over and over.
Don’t check the filter. Dirty and clogged filters are the cause of half of spray equipment problems. Technicians should be checking filters on power and manual sprayers regularly.
Don’t inspect equipment before driving off. Our shop repairs a lot of equipment, mainly backpacks and compressed air sprayers, because equipment comes loose and bounces around the vehicle. We have seen spray guns that have bounced out of vehicles (usually trailers) and were dragged down the road.

Don’t recalibrate sprayers. Just because you calibrated it last year, doesn’t mean you are still putting down the same amount of chemical.
Ignore warning signs. Lots of equipment have warning signs that there is or will be a problem. Too many technicians ignore these signals. Some examples: sprayer hard to pump, small leak, hose blemishes, etc.
Don’t clean/replace spray tips. Spray tips wear out at about 10 percent a year. That means each year a tip puts out 10 percent more product. It is much cheaper to replace the tip.
Don’t do preventive maintenance (PM). No one likes doing PM. It isn’t fun, it doesn’t put money in your pocket now and it takes time. Your equipment will be down for repairs. But it is better that you determine when this occurs.
2. Insufficient Training.
Don’t assume technicians know how to use your equipment and don’t assume that because you trained Johnny five years ago, he is still doing what you want him to do.
Don’t anticipate problems. A lot of equipment problems could have been prevented with just a bit of anticipation and awareness. If a technician sees a piece of equipment or component starting to show signs of wear, it is common sense to assume this will get worse and cause a problem. You know what they say about common sense.
Don’t report problems. Too many technicians will live with problems rather than report or deal with them. A couple of truths in pest control equipment:

- Small problems ALWAYS become big problems.
- Big problems ALWAYS cost more and take more time to fix.
- Big problems ALWAYS occur when you can least afford them.
Don’t understand how equipment works. Technicians don’t always understand how equipment works, which can make finding and diagnosing equipment problems more difficult. Here are some examples:
- A technician points to a pump and says “my motor isn’t working.”
- A technician finds a crack in power sprayer filter. To “solve” the problem, technician puts a piece of duct tape on the crack on the inside of the filter. Duct tape is not the way to fix a filter, but had the technician understood that the pump sucks water through the filter, he would have put the tape on the outside of the filter.
Use wrong or incorrect product in equipment. We have seen strange things. One technician put a couple gallons of bird gel in a power sprayer thinking he would save application time. There was no way to get it out. The tank had to be replaced. Another technician put bleach in his compressed air sprayer. The brass wand was not long for this world.
Only use PPE when applying chemicals. The law requires we use PPE when applying chemicals. Common sense requires we use it whenever we are exposed to chemicals. We often see technicians ignoring PPE when not spraying. Examples are carrying a leaking spray gun into a shop for repairs, unrolling leaking hose to show shop mechanics where to make repairs, etc.
3. Too Rough on Equipment.
Sometimes technicians are downright brutal with equipment.

Pressure too high. Technicians often over-pressurize manual sprayers or turn the pressure up on power sprayers. This is often unnecessary and can reduce equipment life. In the case of power sprayers, drift can occur at higher pressure.
Spray wand as pry bar. Using your manual spray wand to open gates, cabinets or otherwise push stuff out of the way is a sure way to reduce equipment life.
Careless power spray hose rollup. We have seen numerous trucks with paint damage where careless technicians did not bother to ensure the hose cleared the vehicle, damaging both the vehicle and the hose.
Power sprayer hose reels are generally pretty durable (other than o-rings). One way to beat up a reel is to carelessly roll up all the hose so it is unbalanced on one side of the reel. When the reel is rotated with too much hose on one side, the hose pushes the reel out of true and it is almost impossible to fix without expensive repairs.
4. Don’t Take Care of Equipment.
What’s the phrase? An ounce of prevention…
Freeze damage. Winter comes every year, still every year we get calls about freeze damage to pest control equipment.
Don’t clean it out. Cleaning out your equipment is one of the best ways to prevent problems. Most pest control technicians don’t bother. Aside from dirt and chemical residue, the paper liner from chemical bottle lids is a frequent visitor to sprayer tanks.



Rusted out toolbox. A very fastidious technician would wash out his toolbox each week. Problem was, he never bothered to dry it out. The bottom of the toolbox completely rusted out.
Melted backpack. A technician left his expensive Swiss backpack too close to his power sprayer engine exhaust. The backpack melted, dumped two gallons of chemical, technician had to drive to our shop to spend owner’s money on another backpack, all while missing a couple of stops.
Lost gas cap. Lost engine gas caps often mean water in the gas, which usually means an hour cleaning the carburetor.
5. Attitude.
Attitude is a little thing that makes a big difference.
Truck as a trash can. This one is particularly frustrating. Technicians who use vehicles, or even power spray tanks, as trash cans. The strangest things we have found in tanks: engine pull cords, beer cans and a pair of men’s underwear.
Bad attitude. Finally, the most common issue seen in our shop is technicians who don’t take responsibility for their equipment, their error or their problems. It is always someone else’s fault: the manufacturer, the guy who sold it, the mechanic who repaired it, another technician, etc.

RECOMMENDATIONS. Skill and training issues are easier to fix than bad attitude issues. Every manager out there is complaining about the tough hiring environment. Finding good people is tough and getting tougher, which may cause some of these problems to get worse. Most of the solutions to the issues listed previously are HR-related issues rather than equipment-related issues.
Train and retrain. Training is never done. Every month share an idea or training tip.
Assign responsibility and hold technicians accountable. Equipment that is shared is no one’s responsibility and quickly becomes junk. Assign a specific piece of equipment to a specific technician and hold him/her accountable for it.
Ask employees for ideas/feedback. Technicians use the equipment every day. Owners and supervisors aren’t in the field and don’t have all the answers.
Supervisor/manager/owner ride-a- longs. Periodically ride with technicians to see what their day is like and what it is like to actually use the equipment in the field.
Make it easy for customers to contact/complain. Customer complaints can be a good sign you have a problem. Make it easy for customers to complain. Ask for their feedback. Use multiple methods (e.g., phone, email, text, etc.). Remember, you would rather have them tell you of a problem than post it on social media.
Where there’s smoke, there’s fire. Take action at the first sign of trouble. Hire slow. Fire fast.
Vehicle inspections. Conduct regular vehicle inspections. Create a checklist to make it easy. Track results. Hold technicians accountable.
Repercussions for problems, rewards for great work. If you reward a technician for having a perfect vehicle inspection or spotless equipment, you likely will get more of this. Conversely, if technicians see you don’t hold Johnny accountable for the terrible condition of his equipment, they will think it doesn’t matter and may follow suit.
Andrew Greess is president of pest control equipment website Qspray.com and author of “Stop Spraying Money Down the Drain,” a reference guide for pest management and lawn care professionals.
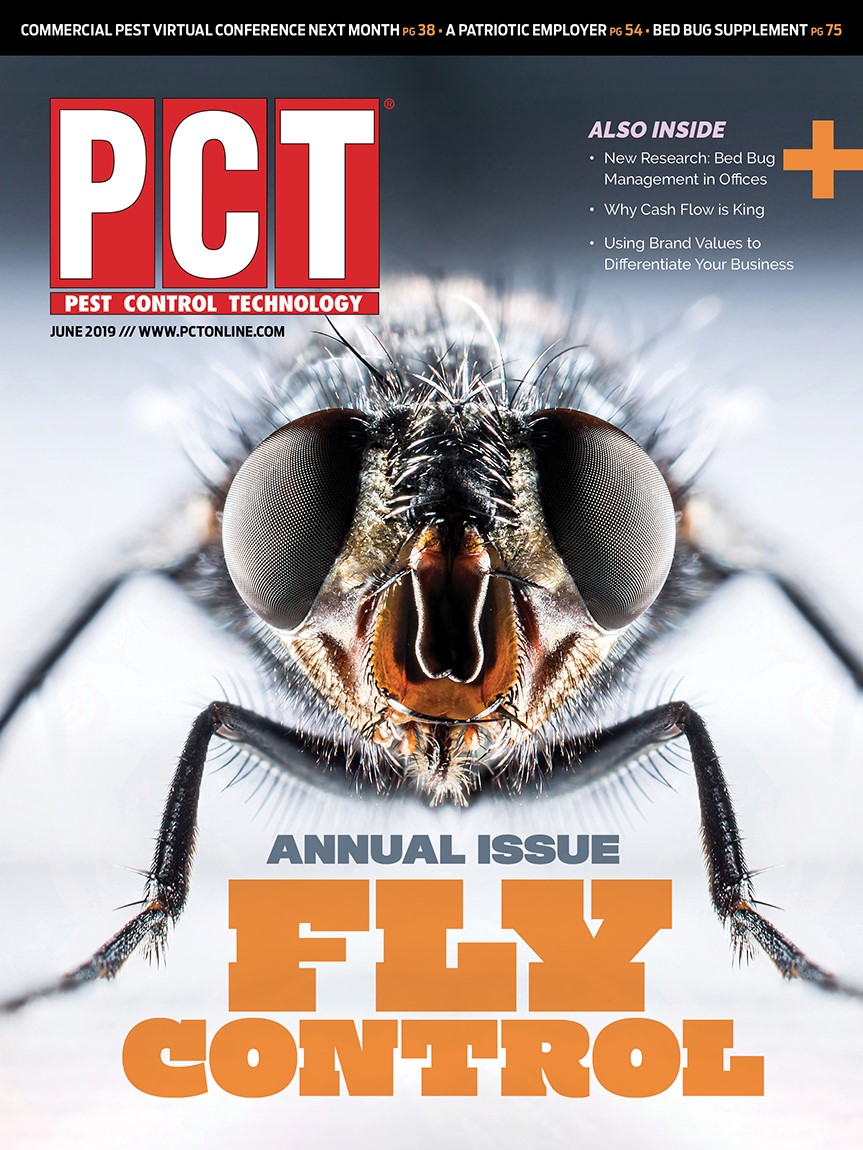
Explore the June 2019 Issue
Check out more from this issue and find your next story to read.
Latest from Pest Control Technology
- SiteOne Hosts 2024 Women in Green Industry Conference
- Veseris Celebrates Grand Reopening of the Miami ProCenter
- Rollins' 2024 Second Quarters Revenues up 8.7 Percent YOY
- Fleetio Go Fleet Maintenance App Now Available in Spanish
- German Cockroach Control Mythbusting
- Total Pest Control Acquires Target Pest Control
- NPMA Workforce Development Shares Hiring Updates
- Certus Acquires Jarrod's Pest Control