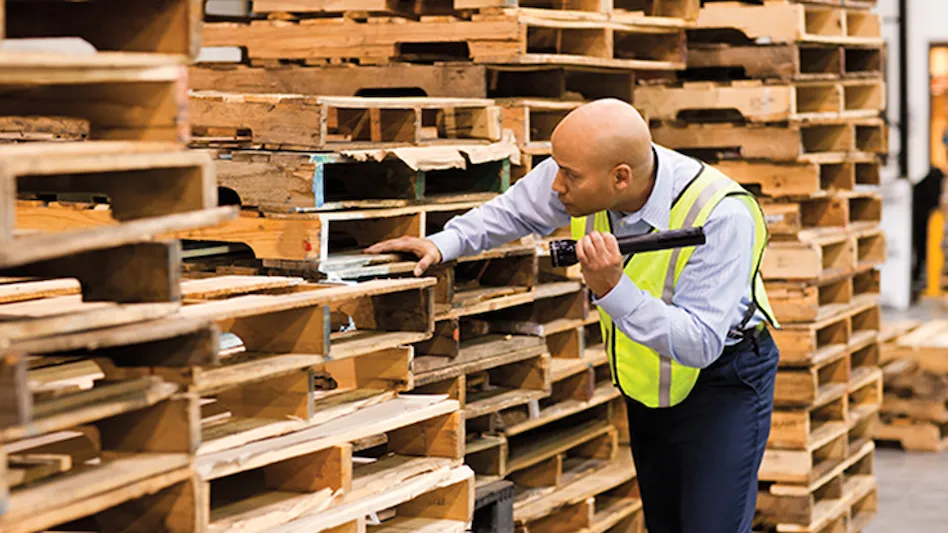
In today’s food safety- and quality-driven environment, third-party audits have become a daily reality for food-processing, packaging and warehousing facilities. Increasingly, audits are moving toward standards accepted around the globe, such as Global Food Safety Initiative (GFSI)-recognized schemes including SQF, BRC and FSSC 22000.
While pest management is a smaller portion of any overall audit, it is a critical one. Pest management is a prerequisite program that must be in place — in other words, pest management is fundamental to food safety. I’ve been auditing food-processing facilities for more than a decade, including more than five years in GFSI standards. I’ve seen a lot of great pest management efforts, but I’ve also seen some things that made me raise my eyebrows.
Lapses in either program details or documentation may result in lost points, as well as heightened scrutiny by auditors in other areas of the audit. The general question in my mind as an auditor is, “If the fundamentals aren’t right, where else are there gaps?”
In the past, many third-party-audit pest control requirements were very prescriptive — for example, bait stations were to be placed a certain number of feet apart no matter what the facility was. But, as audits move toward requiring risk-based pest management programs, these standard requirements that allowed facilities and pest management providers to “check a box” are quickly going away.
Facilities need to partner with their pest management providers to develop tailored programs — and that means addressing specific risks and concerns present at each facility. For technicians and pest management providers, that means having advanced knowledge of the standard to which the facility is being audited and staying up to date on changes to that standard over time.
It is equally important that the pest management provider be familiar with the facility layout, as well as with the products that facility is producing and its processes to best identify areas of risk. Then, the pest management provider must continually evaluate the program and make adjustments as conditions at the facility change to ensure the program remains effective.
I’ve laid out three scenarios that I have seen in my audit experience — and the results for the facility. Do your clients have similar conditions or areas of risk? What are your team members doing to ensure a result like scenario three?
If these types of facilities are in your client roster, you and the team members providing service should be audit experts. Know the types of audits your facilities face and make sure the programs you implement meet the minimum requirements of those standards. Pest management, while ultimately the facility’s responsibility, is a critical baseline to get right. If points are lost in pest control during an audit at one of your clients today, you may be out of a job tomorrow.
Scenario 1
While performing a tour of storage areas at a pouched rice, soup and ready-to-eat meal manufacturer during an FSSC 22000 audit, I observed a pallet of product without any type of marking on it. There was substantial insect activity, as well as evidence of rodent activity. It was apparent during inspection that the pallet had been sitting undisturbed for some time.
As it turns out, the pallet of product was used for testing purposes. No products going to consumers were contaminated, and there was no evidence of live rodent activity. However, I had to score it as a major non-conformance to the standard.
The result was that the facility had to go through a full root-cause analysis, and show evidence of correction and corrective action implementation. The facility was lucky — it could have led to a certification suspension had this been consumer product or evidence of live rodents was noted. It also could have resulted in a revisit for the facility, with all the associated costs. These things may have resulted in loss of customers for this particular facility.
Scenario 2
I was conducting an SQF audit at a warehouse facility that was using a small local pest management provider. All documentation was kept by hand, rather than electronically.
While the standard does not require electronic documentation, the facility had a difficult time producing tracking and trending results. Without these, there was no way to document effectiveness of the pest management program.
This lack of easily accessible documentation was cause for a minor non-conformance and a one-point deduction in the pest control section of the audit. That one point was added to several other deductions at the facility, which resulted in a “surveillance” audit to be conducted six months later. Had the pest management provider been familiar with the standard, they may have been able to put together tracking and trending by hand or make a small investment in software to easily produce the information, eliminating a major headache for their customer.
Scenario 3
While auditing a vegetable-processing facility that had several high- and low-risk areas, the facility had comprehensive documentation readily available for review, including a detailed risk assessment that was reviewed annually by the pest management provider. There was also documentation that the pest management provider had trained facility employees on traps and stations, what should be done if pests or activity were observed and how to handle loose pesticides.
With all of these records easily accessible, well organized and complete, the documentation was easy to evaluate and demonstrated to me that there was a true commitment to the success of the pest management program. The subsequent facility review backed up the documentation.
This facility received an “excellent” rating in the audit.
About the author: Kris Middleton, Hon. B. Sc. is the AuditReady Program Manager for The Steritech Group, Charlotte, N.C. Middleton has more than a decade of experience in auditing food and packaging manufacturers, and has spent the last five years focused on SQF and FSSC 22000.
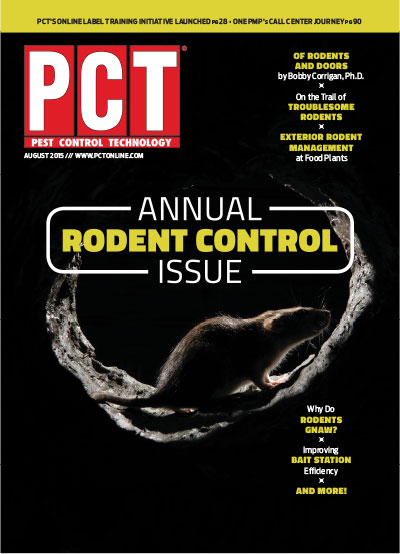
Explore the August 2015 Issue
Check out more from this issue and find you next story to read.
Latest from Pest Control Technology
- Viking Pest Control Organizes a Charity Bike Build for Local Families
- Gaining Control of Structure-Infesting Carpenter Ants
- Big Blue Bug’s Brian Goldman Receives Rhode Island Small Business Person of the Year Award
- UF Researchers Examine How Much Bait it Takes to Eliminate a Subterranean Termite Colony
- Women in Pest Control Group Continues to Grow, Provide Opportunities in the Industry
- NPMA Announces Results of 2024-2025 Board of Directors Election
- Massey Services Acquires Orange Environmental Services
- Hawx Pest Control Wins Bronze Stevie Award for Sustainability